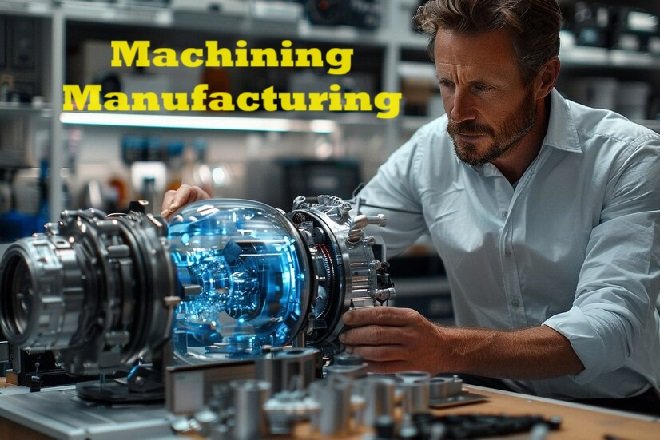
The machining manufacturing industry is crucial to the global economy, supporting sectors like automotive and aerospace. With rapid technological advancements, staying updated on trends is vital. This blog post discusses the industry’s current state, challenges, opportunities, and emerging trends, offering insights for both seasoned professionals and newcomers to drive business growth.
Understanding the Machining Manufacturing Industry
The Foundation of Modern Industry
Machining manufacturing is the process of shaping and manipulating materials to achieve desired specifications. This involves various techniques such as turning, milling, drilling, and grinding, which are instrumental in producing everything from intricate components to large-scale machinery. Heavy equipment manufacturers rely on this industry, which is crucial not only for creating finished products but also for maintaining and repairing.
The global machining manufacturing market continues to grow, driven by demand for precision and efficiency. In 2021, the market was valued at approximately $600 billion and is projected to expand as economies recover and technology evolves. For professionals in the field, understanding the foundations and the critical role machining plays in manufacturing is vital to navigating the complexities of today’s marketplace.
Key Challenges Faced by the Industry
Despite its importance, the machining manufacturing industry faces several challenges. Supply chain disruptions, workforce shortages, and rising material costs are just a few of the hurdles manufacturing professionals encounter. The COVID-19 pandemic has exacerbated these issues, forcing companies to adapt quickly to changing conditions.
Additionally, maintaining quality while scaling production remains an ongoing concern. Manufacturers must find innovative solutions to improve efficiency without compromising on quality, a delicate balance that requires thoughtful strategy and execution.
Opportunities for Growth and Innovation
While challenges abound, opportunities are also emerging. The industry’s push towards automation and digital transformation presents an exciting prospect for growth. With advancements in technology, companies can streamline operations, reduce costs, and enhance productivity.
Furthermore, the increased focus on sustainability is driving innovation within the sector. Manufacturers are increasingly seeking ways to minimize their environmental impact, paving the way for sustainable practices that align with consumer expectations and regulatory standards.
Top Trends Shaping the Future of Machining Manufacturing
Automation and Industry 4.0
Automation is at the forefront of the machining manufacturing revolution, thanks to Industry 4.0. This term describes the current trend of automation and data exchange in manufacturing technologies, which encompasses the Internet of Things (IoT), cloud computing, and artificial intelligence (AI).
By implementing automated systems, manufacturers are improving precision and efficiency on the shop floor. Robotic process automation (RPA) can handle repetitive tasks, allowing human workers to focus on higher-level responsibilities. This not only enhances productivity but also reduces the likelihood of human error, a critical factor in maintaining quality standards in machining.
Companies that have adopted Industry 4.0 principles are already seeing tangible benefits. For example, a leading automotive manufacturer integrated IoT sensors into its production line, enabling real-time monitoring and predictive maintenance. This transition resulted in a 15% increase in production efficiency and a significant reduction in downtime.
Sustainable Manufacturing Practices
In an era where consumers are increasingly conscious of environmental impact, sustainable manufacturing practices are no longer optional; they’re essential. The machining manufacturing industry is evolving to include eco-friendly processes and materials, which not only benefit the planet but also enhance brand reputation and customer loyalty.
Sustainability initiatives can include using renewable energy sources, recycling materials, or implementing waste reduction strategies. For instance, some manufacturers are adopting closed-loop systems that allow them to recycle scrap material back into the production process, significantly reducing waste.
Not only do sustainable practices contribute to a healthier environment, but they can also lead to cost savings. By optimizing resource usage and minimizing waste, companies can lower operational costs while meeting regulatory requirements.
Advancements in Tooling Technology
The tooling technology used in machining is undergoing rapid advancements that promise to enhance efficiency and quality. New materials, such as ceramic and composite tooling, offer greater durability and performance compared to traditional options. These innovations allow for longer tool life and reduced downtime, resulting in increased productivity.
Additionally, the rise of smart tools embedded with sensors provides manufacturers with valuable data analytics. This technology can monitor tool wear in real time, enabling timely replacements and maintenance. By integrating smart tooling technology into their operations, manufacturers can optimize performance and reduce waste.
For example, a manufacturer specializing in aerospace components adopted advanced tooling solutions that improved tool life by 25%. This not only reduced costs but also allowed for the consistent production of high-quality parts.
The Rise of Customization and Additive Manufacturing
Customization is becoming increasingly important in today’s marketplace, as consumers seek personalized products that meet their unique needs. Additive manufacturing, commonly known as 3D printing, is a game-changer in this regard. It allows for rapid prototyping and production of customized components without the need for extensive tooling.
This trend has profound implications for the machining manufacturing industry. Companies can now produce small batches of customized parts more efficiently, reducing lead times and costs. The versatility of additive manufacturing also enables the exploration of complex geometries that were previously impossible to achieve with traditional methods.
A notable example of this trend is the medical device industry, where custom implants and prosthetics are produced using 3D printing. This approach not only improves patient outcomes but also demonstrates how customization can revolutionize traditional manufacturing processes.
Driving Innovation and Reducing Costs
The trends shaping the machining manufacturing industry contribute to innovation while simultaneously reducing costs. Automation increases productivity and minimizes errors, resulting in substantial savings over time. Sustainable practices lead to lower waste disposal expenses and energy savings, while advancements in tooling technology enhance efficiency.
Furthermore, the rise of customization allows manufacturers to tap into new markets, meeting consumer demands and driving revenue growth. By staying ahead of these trends, companies position themselves for long-term success.
Conclusion
The machining manufacturing industry is evolving rapidly, influenced by automation, sustainability, advancements in tooling technology, and the rise of customization. By understanding and adapting to these trends, manufacturing professionals and industry innovators can drive innovation, enhance efficiency, and secure a competitive advantage.