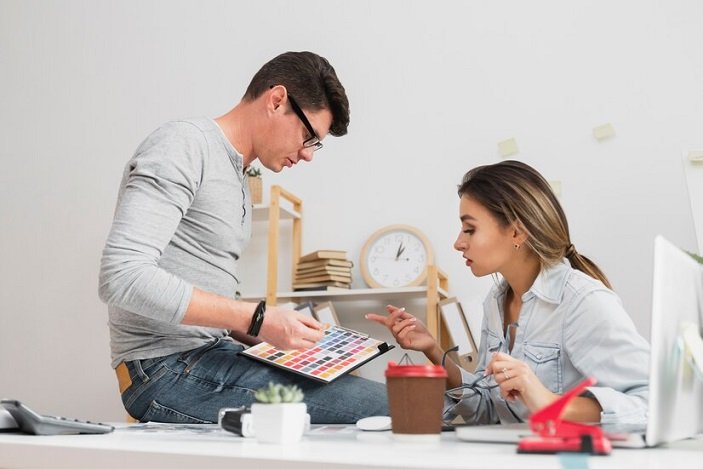
Choosing the correct size of rivets is crucial for any project involving securely fastening materials together. They come in various sizes, each designed to accommodate specific needs based on the materials being joined and the strength required. Understanding these factors not only enhances the effectiveness of your assembly but also contributes to the overall durability and reliability of the finished product. This article will help you through the steps to make sure you choose the right size for your project.
Key Dimensions of Rivet Sizing
The size of the rivet nut is determined by several key dimensions: diameter, length, and grip range. Diameter refers to the width of the shaft, which correlates with its strength. Larger-diameter ones generally provide greater strength and load-bearing capacity. Length refers to the total thickness of the materials that the rivet can securely join. Grip range is the maximum and minimum thickness of materials that the rivet can effectively fasten together.
Assessing Material Compatibility
The first step in choosing the right size is assessing the materials you intend to fasten. Different materials have varying strengths and thicknesses, directly influencing the type and size needed. For example, a small-diameter rivet nut with a short grip range would be suitable if you’re joining thin aluminum sheets. In contrast, joining thicker pieces of steel might require a larger diameter with a longer grip range to ensure a secure connection.
Determining Load Requirements
Consider the load or stress that the joint will experience during its intended use. Rivet nut inserts are used in applications ranging from lightweight crafts to heavy-duty construction. For structural integrity and safety, it’s essential to match their size to the anticipated load. High-stress applications typically require larger and stronger rivets to withstand the forces involved.
Consulting the Size Charts
Many manufacturers provide detailed size charts that specify the recommended sizes based on material thickness and application. These charts are invaluable tools for quickly identifying the appropriate diameter and length for your project requirements. Referencing these charts ensures that you choose a blind nut that meets your structural needs and industry standards, facilitating precision and efficiency in your assembly process.
Considering Head Styles
Rivet heads come in various styles, including dome, countersunk, and large flange. The choice of head style depends on the aesthetic and functional requirements of your project. Dome heads are often used for general-purpose applications where a smooth finish is desired. Countersunk heads sit flush with the surface, which is ideal for applications with a flat surface. Large flange heads not only distribute the load over a larger area but also enhance the stability and resistance of the joint, making them suitable for applications requiring added strength and durability.
Testing and Prototyping
Testing and prototyping before committing to a large-scale fastening operation is crucial for ensuring the reliability of your joints. This process enables you to evaluate how well different sizes and materials perform under real-world conditions, allowing you to make informed selections that enhance the overall quality and longevity of your project. By conducting thorough testing, you can identify potential weaknesses and optimize your fastening solutions for optimal performance. Moreover, it provides a controlled environment where adjustments can be made to improve efficiency and durability, ensuring that the final application meets or exceeds expectations for safety and functionality.
Choosing the right size of rivets for your project involves careful consideration of material compatibility, load requirements, and sizing standards. By understanding these factors and utilizing the size charts, you can confidently select rivets that provide optimal strength and durability for your specific application. Whether you’re embarking on a DIY project or overseeing a large-scale industrial operation, the right size is essential for achieving secure and long-lasting fastenings.