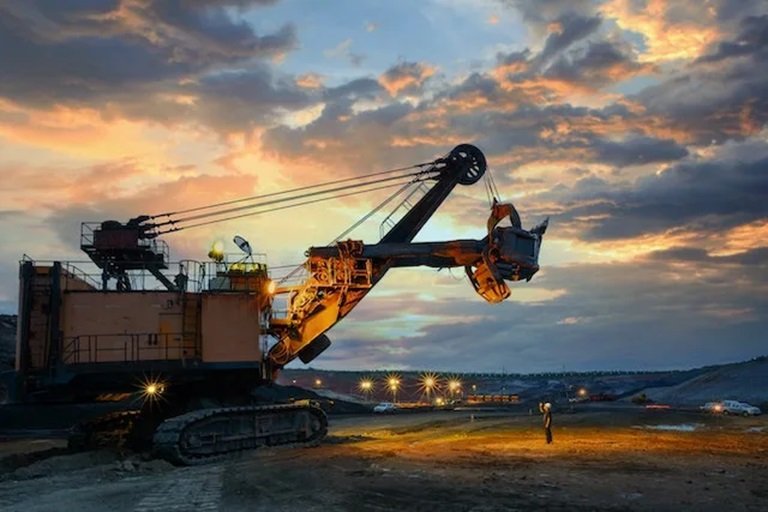
Lifting slings are crucial tools in various industries for safely moving heavy loads. But are you confident in using them correctly? Mistakes in their use can lead to accidents, equipment damage, or even injury. Understanding the common pitfalls can help prevent these issues and ensure a safe working environment.
Misjudging the Weight of the Load
One of the most common errors is misjudging the weight of the load. Underestimating the weight can overload the sling, which might fail. Always verify the weight of the load before selecting lifting slings. Manufacturers provide weight limits for different slings, so it’s essential to stay within these guidelines to avoid accidents.
Using the Wrong Type of Sling
Different types of slings are designed for various applications. Selecting the wrong type of sling for a specific job can be a critical mistake. For example, synthetic slings are not suitable for high-temperature environments, while chain slings may not be ideal for lifting fragile items. Understanding the properties and limitations of each type is key to ensuring safe and effective lifting operations.
Synthetic Slings vs. Chain Slings
Synthetic Slings are lightweight, flexible, and ideal for delicate loads. However, sharp edges or extreme temperatures can easily damage them, so it’s vital to inspect synthetic slings regularly for signs of wear and tear.
Chain Slings: Known for their strength and durability, they are suitable for heavy and abrasive loads. However, they require regular maintenance to prevent corrosion and wear.
Improper Sling Angle
The angle at which a sling is used significantly affects its lifting capacity. A common mistake is using the sling at an incorrect angle, reducing its capacity and increasing the risk of failure. The greater the angle from the vertical, the more stress is placed on the sling. Always aim to use the sling at an angle of 90 degrees to maximise safety and efficiency.
Ignoring the Importance of Inspection
Regular inspection of slings is crucial for maintaining safety. However, it’s often overlooked or performed inadequately. Failing to inspect slings before each use can lead to undetected damage or wear, which increases the risk of accidents. Look for signs of fraying, cuts, corrosion, or any other form of damage. If any defects are found, the sling should be taken out of service immediately.
What to Look for During Inspection
Fraying or Cuts: Check for any visible damage to the fibres or links of the sling. Even minor fraying can compromise the integrity of a synthetic sling.
Corrosion: Corrosion can weaken metal slings, making them less reliable. Regular cleaning and proper storage are important to prevent this.
Distortion: Ensure that the sling retains its original shape. Any bending or distortion can indicate that the sling has been overloaded in the past.
Misuse of Hardware and Attachments
Using the wrong hardware or attachments with lifting slings is a common mistake that can compromise safety. Ensure that shackles, hooks, and other attachments are compatible with the sling. Also, they should be inspected regularly for wear and tear. Using incompatible or damaged hardware can lead to failure during lifting operations.
Ensuring Compatibility
Shackles: Choose shackles that match the sling’s size and capacity. They should fit snugly without putting undue stress on the sling.
Hooks: Hooks should be large enough to accommodate the sling without causing damage. Avoid hooks with sharp edges that could cut into the sling material.
Lifting slings are vital for safe material handling, but their effectiveness depends on proper use and care. You can enhance safety and efficiency in lifting operations by avoiding common mistakes such as misjudging load weight, using the wrong type of sling, improper sling angles, and neglecting regular inspections. Proper training, maintenance, and adherence to guidelines will help prevent accidents and prolong the lifespan of your equipment.