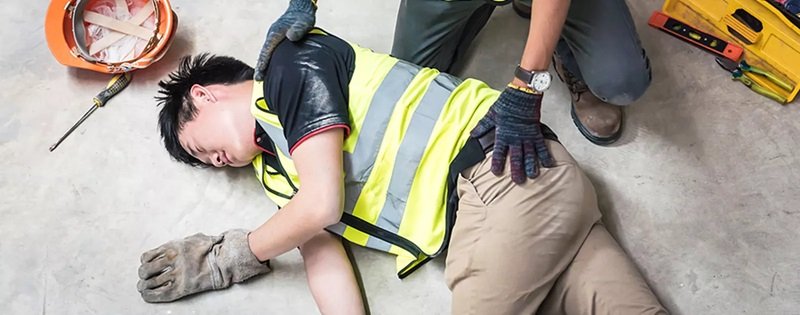
At work, employee safety should always come first. With asbestos being one of many potential workplace dangers that pose risks to employee health, asbestos removal is essential in protecting workplace security and employee wellbeing Workplace Hazards. Let’s examine five common hazards with strategies on how best to avoid or mitigate them for an enjoyable work experience for all employees.
1. Slips, Trips and Falls Workplace Hazards
Slips, trips & falls remain an inherent danger of working environments in all industries or settings; no matter whether it be industry-specific. Such incidents frequently result from minor hazards like wet floors, cluttered pathways, or tangled cords which pose potential threats that often go undetected until too late to prevent injury Workplace Hazards.
Accidents may seem innocuous at first; however, even seemingly minor events can have devastating results and result in permanent disabilities if left unaddressed Workplace Hazards.
To effectively mitigate their potential effects, proactive steps must be taken; such as promptly cleaning up spills and clearing away hazards from pathways.. Implementing non-slip flooring and providing appropriate footwear can greatly decrease the chance of slips and falls, and regular facility maintenance including routine checks for hazards combined with adequate lighting can further bolster workplace safety Workplace Hazards.
Fostering an environment of safety among employees is integral. Encouraging staff to report potential hazards promptly can prevent accidents before they happen; providing regular safety training sessions on maintaining an accident response protocol also plays a crucial role. By prioritizing safety and taking preventative steps, workplaces can substantially decrease slips, trips, and falls and create an overall safer working environment Workplace Hazards.
2. Ergonomic Risks
Ergonomic risks pose significant threats to employee health and well-being, often leading to musculoskeletal disorders and chronic pain. They stem from poor workplace design–insufficient workstation setups or seating arrangements, for instance–thus making these hazards even harder to avoid. Addressing ergonomic concerns involves physical changes as well as education about them: providing adjustable workstations or ergonomic furniture allows employees to customize their workspace according to individual needs Workplace Hazards for comfort while decreasing injury risks; encouraging regular breaks with proper posture practice can further mitigate them by relieving strain off of their body!
Conducting regular ergonomic assessments is vital to quickly recognizing potential hazards and taking immediate corrective actions against any possible dangers that might emerge, while at the same time providing employees with adequate ergonomic training programs to recognize and address ergonomic issues at work effectively, thus creating a culture of safety and wellbeing in their workplaces.
Prioritizing ergonomic issues while taking preventative steps helps employers safeguard employees against potentially detrimental ergonomic risks, creating healthier employees who ultimately provide greater productivity overall.
3. Chemical Exposure
Exposure to chemicals poses serious health hazards in the workplace. From cleaning agents and industrial chemicals, improper handling may cause skin irritation, respiratory difficulties, and long-term health effects that require long-term medical treatments. To guard against chemical exposure effectively in your organization, implement proper ventilation systems and supply sufficient PPE; train employees on safe handling practices (including disposal procedures); perform regular hazard analyses to identify and mitigate all relevant hazards efficiently.
4. Electrical Hazards
Electrical hazards are one of the primary sources of workplace accidents and injuries, from electrical shocks to fires Workplace Hazards. To protect workplace employees against electrical risks and injuries caused by electrical systems, regularly qualified personnel should inspect them using lockout/tagout procedures when conducting repairs or maintenance work; additional training programs on electric safety practices including correct use and identification of potential dangers should also be offered quickly to minimize accidents caused by such electrical incidents as much as possible Workplace Hazards.
5. Asbestos Exposure
One of the primary workplace hazards is asbestos exposure. Once revered for its fireproofing and insulation capabilities, asbestos now poses serious health hazards if disturbed, necessitating its removal for employee wellbeing and employee health safety purposes. Regular professional inspections to identify ACMs should also take place as proper containment procedures can reduce exposure risks further while training employees about handling procedures can educate employees of potential dangers associated with asbestos. Education of employees about asbestos risks will raise their awareness while creating accountability in an organization dedicated to managing asbestos risks efficiently!
Conclusion
Protecting employees against common hazards at work is paramount to creating an efficient and safe working environment for them. By managing risks such as slips, trips, and falls; ergonomic hazards; chemical exposure risks electrical hazards, and asbestos hazards it can protect employee wellbeing while decreasing workplace accidents. Be proactive by undertaking inspections and training employee removal. Together let’s create an environment in which workers thrive without jeopardizing their health or safety!